Precast Concrete Vs. Cast-In-Place: What’s The Difference?
When working on construction projects, concrete is often the material of choice due to its strength, versatility, and durability. However, the method of using concrete can vary significantly. The ongoing debate between precast concrete vs. cast-in-place centers around which method is more efficient, cost-effective, and reliable for different types of builds.
Both methods serve unique purposes in construction with distinct advantages and challenges depending on the scope of the project. As construction technology advances, many contractors are leaning towards one method over the other to enhance quality and shorten project timelines.
Choosing between precast and cast-in-place concrete depends heavily on the project’s requirements, location, and specific challenges. Factors like the size of the components, site accessibility, labor availability, and overall project timeline all play significant roles in determining which method is better suited for a particular job.
While precast concrete is known for its efficiency and consistency, cast-in-place allows for greater customization and adaptability on-site.
At Ernest Maier, we’ve been involved in the world of concrete for decades with solutions for both cast-in-place and precast applications. Whether you need structural elements like concrete lintel beams or large-scale architectural pieces, understanding the differences between these two methods is critical in making the right choice for your project.
Understanding the Basics of Precast Concrete Vs. Cast-In-Place
Before looking into the pros and cons, it’s essential to understand what sets precast concrete apart from cast-in-place concrete. The fundamental difference lies in where and how the concrete is cured. Precast concrete is produced offsite in a controlled environment and then transported to the construction site, ready for installation.
On the other hand, cast-in-place concrete is poured directly at the job site and cured in its final location. These differences in production methods have a profound impact on everything from project timelines to material quality and cost.
The Efficiency of Precast Concrete
One of the most significant benefits of precast concrete is its efficiency. Precast concrete products are created offsite in a controlled manufacturing facility where variables like temperature, humidity, and curing time are carefully monitored. This control promises a more consistent quality across the board.
This reduces the likelihood of defects or weather-related delays. When the concrete elements are delivered to the site, they are ready for immediate installation, significantly reducing the time spent on-site compared to cast-in-place methods.
This efficiency is especially beneficial for large-scale projects that require repetitive structural components. Instead of waiting for each section of the structure to be formed, poured, and cured on site, precast concrete elements such as walls, columns, or lintels can be quickly positioned and connected.
The Customization and Flexibility of Cast-In-Place
While precast concrete offers efficiency, cast-in-place concrete provides flexibility. Since cast-in-place is poured directly into formwork on the job site, it allows for custom shapes and sizes that are specific to the project’s needs. This is particularly advantageous for projects requiring irregular or non-standard shapes that might be challenging to produce in a precast facility.
Additionally, because cast-in-place concrete doesn’t need to be transported, it is ideal for very large components that would be difficult or impossible to move. This method is often used for projects like large foundations, structural slabs, and basement walls. It can be poured and molded to fit any shape or contour. It’s the go-to option for complex designs that demand on-site customization.
Strength and Durability
When comparing the strength and durability of precast concrete vs. cast-in-place, precast concrete tends to have the edge. Since precast concrete is manufactured in a controlled environment, it can be cured under optimal conditions that lead to stronger, more durable elements. The controlled production also allows for the inclusion of prestressed cables; this adds to the overall strength of the final product.
While still durable, cast-in-place concrete is more susceptible to variations in quality due to its on-site curing process. Factors like weather, temperature, and humidity can affect the curing time and the final strength of the concrete.
Additionally, cast-in-place concrete is often reinforced on-site, which can lead to inconsistencies in the final product if not done with precision. When properly executed, cast-in-place concrete can still offer substantial strength. It is preferred for large foundations and heavy structural components.
Quality Control and Consistency
Quality control is another area where precast concrete outshines cast-in-place. The manufacturing of precast concrete takes place in a controlled environment and allows for stricter quality control measures than those typically found on a construction site. Each element is inspected for defects before being transported to the job site so that only high-quality materials are used.
This level of control is difficult to achieve with cast-in-place concrete. External factors such as weather conditions and site limitations can introduce variability in the curing process. While cast-in-place concrete can still achieve good results, it requires more oversight and management on-site to ensure consistency.
Installation Time and Labor Considerations
Time is a critical factor in construction projects. This is where the differences between precast and cast-in-place concrete become particularly apparent.
Precast concrete’s production offsite and in advance means that when it arrives at the construction site, it is ready for immediate installation. This minimizes downtime and allows projects to proceed more quickly, especially in comparison to the extended curing periods required for cast-in-place concrete.
On the other hand, cast-in-place concrete requires additional time on the site for formwork preparation, pouring, and curing. This can be particularly time-consuming on large projects, as each section must be carefully poured and allowed to cure before the next stage can begin. This does not, however, require advanced planning. For projects on a tight timeline, this can be a significant drawback that leads to increased labor costs and potential delays.
Transportation and Logistics
Although precast concrete offers many benefits, transportation is one of the primary logistical challenges. Precast elements need to be transported from the manufacturing facility to the job site. This process can involve additional costs and potential risks, especially for oversized elements. However, for projects located close to the manufacturing plant, these transportation concerns are often minimal.
Cast-in-place concrete eliminates these transportation challenges, as all work is done on-site. This makes it ideal for projects in remote locations where transporting large precast elements would be impractical or expensive or where setting up a crane is difficult.
Cast-in-place concrete can either be ready-mixed or mixed on-site. A delivery vehicle will still need to arrive at the site, and those logistical challenges need to be managed. When a mobile mixer is used the logistics and material management must also take into account cement, sand, and water at the site. This can also present logistical challenges depending on the site’s location and access to resources.
Large-Scale Projects
When it comes to large-scale construction projects, precast concrete has become the preferred choice due to its ability to reduce onsite labor, speed up the construction timeline, and provide high-quality, durable products. Repetitive elements such as parking structures, retaining walls, and structural beams are ideal candidates for precast concrete. These components can be manufactured en masse for consistency and to reduce costs through economies of scale.
Precast concrete is also favored for projects that are well-planned and regular in nature. This includes large infrastructure projects, commercial buildings, and industrial facilities. Its durability and ability to be reinforced make it ideal for structures that must withstand heavy loads or environmental stressors.
Cost Considerations
Cost is a major factor when choosing between precast and cast-in-place concrete. Precast concrete typically has higher upfront costs due to the need for offsite manufacturing and transportation. However, this is often offset by the reduced time and labor costs associated with the installation process. The quicker installation process can lead to savings on labor where the cost of pouring, curing, and finishing cast-in-place concrete can quickly add up.
While initially more affordable in terms of material and labor, cast-in-place concrete can become more expensive over time. This can be due to extended project timelines, potential delays, and the need for additional labor to manage the curing and reinforcement process. Additionally, any issues with the quality of the cast-in-place concrete can lead to costly repairs or future maintenance expenses.
Environmental Impact
This is pretty even between the two options.
Precast concrete has less waste, because of its controlled production process. The reduction in on-site labor and shortened project timelines also contribute to its overall sustainability, as fewer resources are required to complete the project.
Cast-in-place concrete tends to take advantage of optimized mix designs and material innovations. It also avoids a lot of transportation and logistics-related emissions by being sourced locally.
In the debate between precast concrete vs. cast-in-place, the right choice ultimately depends on the specifics of the project at hand. Precast concrete offers unparalleled efficiency, quality control, and durability. It’s the ideal choice for large-scale projects or those requiring repetitive elements. It also provides environmental benefits and cost savings over time due to its shorter installation times and lower labor costs.
While less efficient, cast-in-place concrete offers greater flexibility and customization. It’s suitable for projects that require unique or large-scale elements that would be difficult to transport. It remains a solid option for foundations, large slabs, and complex designs that need to be tailored on-site.
At Ernest Maier, we provide a full range of concrete products and solutions, including both precast and cast-in-place options. Contact us today to learn more about how we can support your construction needs with high-quality concrete solutions.

SalesZac Bunner
Latest News
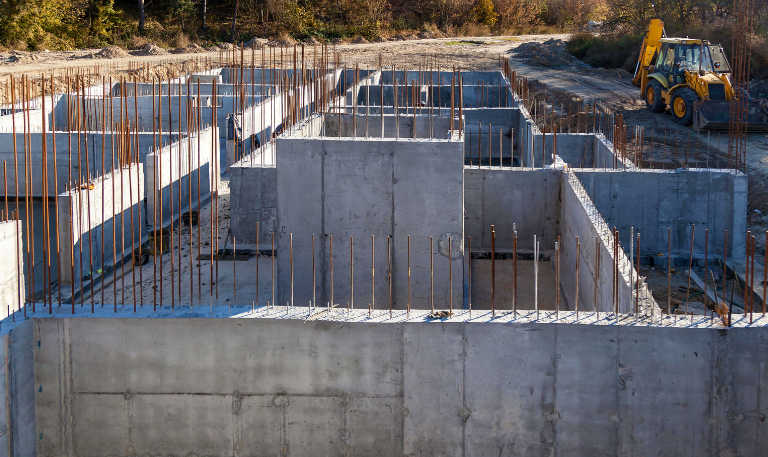
4 Ways To Reinforce Concrete
Concrete is one of the most fundamental materials used in construction. If you’re working on a domestic project or a […]

The Environmental Benefits Of Using Ready-Mix Concrete
The construction industry is changing quickly to meet the growing demand for sustainability and eco-friendly practices. One of the most […]
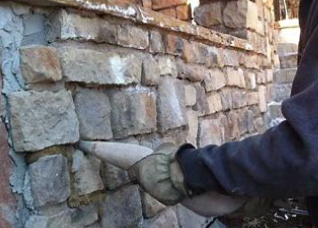
6 Essential Tips For Grouting Stone Veneer
Grouting stone veneer is an important step in the installation process that can significantly impact the overall look and durability […]

Should You Fill Hollow Concrete Blocks?
Hollow concrete blocks are widely used in construction due to their strength, versatility, and lighter weight compared to solid blocks. […]